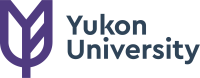
Whitehorse Copper
Little Chief Deposit
Site Introduction
Location (latitude/longitude):
60.641186°, -135.067173°
The Little Chief deposit is the largest ore body in the Whitehorse Copper Belt and provided around 60% of all the copper produced during mining. Although the deposit was one of the first staked in the early 1900's, its relatively low-grade meant that it was not economic given the high costs of underground mining, and it was not mined.
More than half a century later, modern exploration methods outlined a deposit that was suitable for lower-cost open-pit mining. Production commenced in 1967, with open-pit mining continuing until 1969. Drilling from the bottom of the Little Chief pit outlined additional ore resources and 7.4 million tons were subsequently mined with underground methods between 1972 and 1982. Collectively, these surface and underground operations at Little Chief and the adjacent Middle Chief deposit were known as "Whitehorse Copper." Ore from smaller open-pit mines in the Whitehorse Copper Belt (Arctic Chief, War Eagle, Keewenaw, Black Cub) was transported to the Whitehorse Copper site for milling and tailings disposal.
Overview map showing the main features of the Whitehorse Copper mine site.
The Mining Cycle
Learn about the stages of mineral exploration and mining at Whitehorse Copper in the series of panels below. The will provide some valuable context for the features that you see in the Whitehorse Copper tour, and at other sites throughout the Whitehorse Copper Belt.
Mineral Exploration
The mining cycle always starts with mineral exploration - the art of finding a new ore deposit. Geologists, scientists trained in identifying and interpreting rocks, go into the field to look for economically valuable minerals and map their distribution. This work is often done in very remote areas with little infrastructure, so it involves lots of hiking, travel by helicopter, camping, and carrying all the necessary tools and supplies with you. The work of the geologist is often aided by geophysical techniques that help map rock and mineral distribution by detecting certain fundamental rock properties, such as magnetism or ability to conduct electricity.
Geologists collect many rock and soil samples in the field, and those samples are sent to a lab for geochemical analysis (or assay). Samples are collected on the surface and also from the subsurface drilling, collecting samples called rock core. Using surface and subsurface samples in conjunction, the mineralogy and geochemistry of these samples allow geologists to define the distribution of rock units and mineralization in three-dimensions. This allows the geologists to develop robust estimates of how much metal is contained within a mineral deposit. If the deposit is deemed economic, it can be called an ore deposit.
Even when a mine has been developed and production is taking place, exploration doesn't end. Exploration geologists continue to try to expand the bounds of known mineralization and increase the mineral resource estimate. This is critical for extending the life of the mine.
Mining Methods
Once an ore deposit has been defined during advanced-stage exploration, a different team of professionals (including environmental scientists, economists, engineers, etc.) will look at the financial and technical feasibility of mine development, plus its environmental and socio-economic impacts. A project that is still prospective given those considerations will be submitted to government permitting bodies, and only after extensive review and consultation may a project be approved for mine construction. The construction phase itself will often take many years!
Mining can take place either as surface (open-pit) mining or underground mining. Open-pit mines are often developed where the orebody is large, low-grade, and relatively close to the surface. These are often called "bulk tonnage" targets. Underground mining is significantly more expensive than surface mining, and is generally restricted to cases where the ore body is high-grade, deep, and/or mineralization is in discrete lenses or veins.
Most of the ore production at Whitehorse Copper came from underground mining. An underground portal (access point) led to a decline or ramp that gradually descended to the main Little Chief ore body, directly under the Little Chief open pit. While miners and equipment typically used the decline for access, ore was removed using a hoist system in a vertical excavation known as a shaft.
Extraction
Mining engineers will design the underground workings of a mine to maximize the amount of ore that can be recovered, while still leaving enough rock in place to prevent collapse. The zones where rock is extracted are known as stopes, and the support zones are known as pillars. The mine design is continually refined as underground access enables production geologists and mining engineers to get a better understanding of ore distribution and rock stability.
To extract rock from a stope, underground drill rigs drill a series of holes on the rock face. The layout of these holes, and their depth, is optimized to achieve a certain size of fragmented material after the blast, and minimize the damage to the surrounding rock. Blast holes are loaded with explosives, the area is vacated, and then a complex blasting sequence is initiated. Not all charges detonate at once - the order and configuration are also important to optimize the blast.
Once a blast is complete, underground miners will stabilize the area with required rock support. The blasted rock (or muck) is then scooped up from the muck pile and transported either 1) directly to the surface, 2) to a waiting underground haul truck, or 3) to an underground jaw crusher to further reduce the size of the rock fragments. Typically, this initial movement of rock material is done by a loader known as a load-haul dump (or LHD).
LHD loader (Photo courtesy of MinerStuff).
Crushing
The first step in ore processing is crushing. In an underground mine, ore is first transported via haul truck or LHD to a piece of equipment called a grizzly. Ore is dumped onto the grizzly screen, and pieces of ore that are smaller than the aperture size on the screen pass through. Pieces that are larger than the screen aperture are caught in the screen and need to be manually broken. The goal of blast design is to minimize the volume of rock caught in the grizzly.
Grizzly at the Silvertip Pb-Zn-Ag mine, British Columbia. Photo courtesy of Joel Cubley.
Material that passes through the grizzly goes to the primary crusher to reduce the grain size of the material, typically to less than 15 cm in diameter. For surface mines, these primary crushers are typically gyratory crushers , but for underground mines an underground jaw crusher may first be employed. Such was the case at Whitehorse Copper beginning in 1974. The ore was then transported to the surface using equipment known as a skip hoist. Once on the surface, it was conveyed to a gyratory crusher for additional grain size reduction.
Mill processing
In a mine like Whitehorse Copper, crushed ore is conveyed to a mill building (concentrator), where it is first subjected to additional grain size reduction in a grinding circuit. A grinding circuit typically involves 1-2 types of grinding mills, huge metal drums partly filled with metal balls that grind the rock down to a flour-like size (typically less than 0.2 mm in diameter). Semi-autogenous (SAG) mills are typically used first, and have 5-20% steel ball content by volume. These mills rely largely on the impact of rock pieces themselves on surrounding rock to pulverize material. These are followed by ball mills, which have a higher percentage of steel balls (up to 40%) and achieve a finer target grain size.
Ground material is transported to flotation tanks for separation of the valuable ore minerals from the unwanted waste materials (gangue minerals or tails). The flotation tanks are aerated, with bubbles rising to the top of the tanks. Two types of chemicals (or reagents) are added to the slurry of water and ground rock: 1) frothers help stimulate bubble production, and 2) collectors make target minerals aerophilic (or hydrophobic) and preferentially attach themselves to the bubbles. The bubble-rich froth at the top of the tank can be skimmed off - it is highly concentrated in ore minerals.
Following flotation, the concentrate slurry (or pulp) is thickened in a thickening tank. Additional chemicals are added that cause the minerals to settle to the bottom (sedimentation), leaving a clarified H 2 O-rich fluid on the top that can be decanted and reused. The thickened pulp can now be dried and dewatered.
This mill product, known as the concentrate, is packaged and transported offsite. The milling on-site only separates ore minerals from gangue; it doesn't isolate the individual metals (e.g. copper) within those minerals. That is the role of smelting. Whitehorse Copper concentrate was transported on the White Pass & Yukon Railway to Skagway, Alaska, and then shipped south to the Port of Vancouver, British Columbia. It was then transported by rail to a smelter in Flin Flon, Manitoba, where the copper was extracted and refined.
Reclamation
The fine-grained gangue material that is uneconomic is typically deposited in a tailings complex. When the tailings complex is full, an effort is made to revegetate and stabilize the surface of the tailings to minimize erosion of tailings materials. The style of tailings management largely depends on what minerals are in that waste material, and how they might weather and release metals upon interaction with ground water, surface water and the atmosphere. Modern mines in Yukon have a regulatory requirement to leave their sites in a "walk-away" condition. This means the tailings must be left in such a state that does not require continued monitoring, and treatment is not necessary to protect the health of the environment (Yukon Mine Site Reclamation and Closure Policy, 2006).
Mine sites will typically have both tailings complexes and waste rock dumps. These are not the same features. Tailings complexes are filled with fine-grained materials that went through the crushing, grinding and separation processes in the mill. Waste rock, on the other hand, is material that was excavated during mining but was deemed uneconomic by geologists and was not processed further. Waste rock dumps will have much coarser rock samples and thus interact with water and air differently than tails. Both waste rock dumps and fine-grained tailings can be seen on the Whitehorse Copper site.
Virtual Field Trip
Explore the Whitehorse Copper site in our virtual field trip, below. In addition to exploring features around the Little Chief open pit, make sure you click on the Tailings Complex link to explore the extensive tailings ponds and former mill site.
Click anywhere on the site tour to launch it, then make sure to click the full-screen button in the top right corner to get the full experience. Once in the tour, click on individual sites to zoom in further and interact with the site.
Chief Geologist Interview
Join Yukon University geologist Dr. Joel Cubley for an interview with Dave Tenney, the Chief Geologist with New Imperial Mines and Whitehorse Copper Mines from 1970-1982. Mr. Tenney provides invaluable perspective on a broad range of topics including surface and underground mining at Little Chief, processing and transport of ore, and tailings disposal. The interview is split into 1-3 minute clips to focus on individual topics. Dig in!
Historic Image Gallery
Browse through the historic images of the Whitehorse Copper site from around 1968 (during the commencement of open pit mining). Clicking on the "i" button on each image will bring up a brief description. Photos courtesy of the Yukon Archives.
Citations from left to right: 1. Yukon Archives, Whitehorse Copper Mines Limited fonds, acc. 83/66, [80]; 2. Yukon Archives, Whitehorse Copper Mines Limited fonds, acc. 83/66, [329]; 3. Yukon Archives, Whitehorse Copper Mines Limited fonds, acc. 83/66, [38]; 4. Yukon Archives, Whitehorse Copper Mines Limited fonds, acc. 83/66, [809]; 5. Yukon Archives, Whitehorse Copper Mines Limited fonds, acc. 83/66, [36]; 6. Yukon Archives, Whitehorse Copper Mines Limited fonds, acc. 83/66, [324]; 7. Yukon Archives, Whitehorse Copper Mines Limited fonds, acc. 83/66, [315]; 8. Yukon Archives, Whitehorse Copper Mines Limited fonds, acc. 83/66, [319]; 9. Yukon Archives, Whitehorse Copper Mines Limited fonds, acc. 83/66, [682]; 10. Yukon Archives, Whitehorse Copper Mines Limited fonds, acc. 83/66, [663]; 11. Yukon Archives, Whitehorse Copper Mines Limited fonds, acc. 83/66, [763]; 12. Yukon Archives, Whitehorse Copper Mines Limited fonds, acc. 83/66, [762]