From Drains to Gains - Wastewater Empowers Green Hydrogen
Based on https://doi.org/10.1021/acs.est.4c08054

H 2 is an important element of Net-Zero, period.
Direct electrification is difficult, if not impossible, in some end-use sectors, including steel-making, chemical production, long-haul aviation and maritime shipping. But there is a viable solution for decarbonising these end uses – “green” hydrogen and other fuels produced from renewable electricity.
No matter from IRENA's 1.5℃ scenario, or Princeton's Net-Zero America report, H 2 is an important element in hard-to-abate sectors - where direct electrification is hard to achieve.
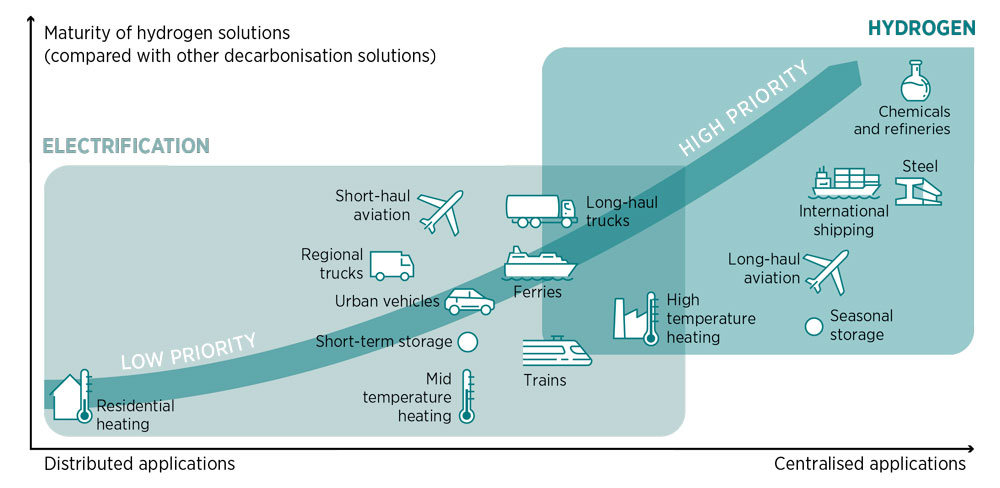
Source: IRENA
Not all H 2 are created equal

Source: Reuters
H 2 comes in many colors - grey H 2 from fossil fuel sources, blue H 2 which is grey H 2 + CCS (carbon capture and storage), and green H 2 which is produced from water electrolysis powered by renewable electricity. Unfortunately, most of the world's current H 2 supply is grey H 2 , with green H 2 expected to take over in the coming decades.
Grey H 2 bears large carbon intensity. With CCS (blue H 2 ), this carbon intensity can be partly offsetted. Green H 2 remains the cleanest method of production with one underlying requirement - the electricity source has to be renewable.
Read more : green H 2 also has a higher tolerance of leakage than blue H 2 to not invoke increase of atmospheric methane - a potent greenhouse gas.
See the below map showcasing all the operational and upcoming electrolyzer projects in the U.S. Data source: IEA Hydrogen Production and Infrastructure Projects Database (Ver. 2023 Oct.).
The water context of green H 2
Although the water consumed for hydrogen production will not have a significant impact globally, the importance of considering local water contexts when planning hydrogen development cannot be overstated, especially chronic water risks such as water stress.
Water is not just needed for electrolysis itself, but for cooling as well. Image Source: Alfa Laval
Water electrolysis - a process that uses electrical energy to break down water molucules to H 2 and O 2 - is a thirsty process as the name suggests. Stoichiometrically, 9 kg of H 2 O is needed to produce 1 kg of H 2 . However, electrolyzers take clean water only - the water purification process itself will have water loss. Then, there is cooling water - water needed to cool down the heat-emitting process. The total demand can ammounts to well over 30 kg of H 2 O per kg of H 2 .
Total quantity-wise, water availability is not a big issue - as the total water demand is significantly smaller than other water-heavy sectors such as agriculture. However, green H 2 can easily become one of the largest water users in a region - pose water stress to local environments and compete with essential water needs.
Unfortunately, one key requirement of green H 2 - renewable energy - often does not come in water-abundant regions.
See the below maps showcasing green H 2 potential from solar and wind (left) and projected U.S. water stress in 2050 (right). Slide around and see for yourself - regions with abudant green H 2 potential are often faced with high water stress.
Reusing wastewater for green H 2 - Because why not?
Across the world, safely reused wastewater is grossly undervalued as a potentially affordable and sustainable source of water, energy, nutrients and other recoverable materials.
For regions that are promising for developing green H 2 but are faced with high water stress, water resource recovery plants, or in short, WRRFs, provide a easily-accessible and viable water options.
See below for a map of WRRFs in the U.S. - they are just about everywhere.
Water Demand of Current H 2 Ssers under Different Water Use Cases and the Flow of Major WRRFs | See data analysis details in the original study.
Besides their convenient location, another prime reason why WRRFs might be a good opportunity to enable green H 2 is - they typically have a much larger water flow than what a H 2 plant would require. This means WRRFs can just provide a slipstream which would be enough to enable green H 2 production without disturbing the original water flow.
But of course, you need to consider a lot of things for water reuse projects: build a water pipe between WRRF and H 2 production site, pumping the water, treating the water...... That's why we built an optimization framework to try to determine whether this is economically feasible, and applied it on the current H 2 producers and WRRFs in the United States. I know - nobody likes to read Methods section, so we saved the boring part in the paper published.
What we found?
Reusing treated wastewater effluents for green H 2 production could save 66% (62% - 99% from the worst case to the best case) of freshwater for the clean hydrogen economy given the current distribution of H 2 producers and WRRFs. States that currently has the highest H 2 activity (such as Texas, Louisiana, California) will benefit the most.
Freshwater Savings for Different States | See data analysis details in the original study.
State-Level Wastewater Flow Diversion under Different Scenarios | See data analysis details in the original study.
The average flow diversion for green H 2 production is < 1.5% on state-level, meaning reusing wastewater effluents for green H 2 production likely will not induce a significant disturbance to the original water cycle.
Minimal Water Selling Price (MWSP) versus the Pair Distance | The green region shows the typical price range for industrial water usage. See data analysis details in the original study.
The calculated minimal water selling price - which is based on the cost of service for providing the reclaimed water - is comparable to, or even lower than, the typical industrial water cost. This means WRRFs can price the reclaimed water provided to the H 2 producers at a profitable yet competitive price.
Further Thoughts
The interaction between WRRFs and green H 2 might be beyond water - the possibilities of tunneling the produced O 2 for aeration, or utilizing the waste heat from electrolyzer are all exciting and worth exploring.
Opportunities of Symbiosis between WRRFs and Green H 2 Production | Visualization by authors using BioRender.
U.S. is mainly operated under two water rights systems - the Riparian Doctrine and the Prior Appriopriation Doctrine. What that essentially means is that WRRFs not necessarily have the right to dispose/use their effluent any way they want. However, many states do have green lights on regarding beneficial reuse. It would be interesting to see how state-level regulations unfold. We are optimistic that such reuse makes economic and environmental sense, and perhaps equally importantly - unlike potable reuse which people always have a hard time accepting, most people don't care if the H 2 they directly or indirectly use comes from freshwater or impaired water at all.
Cite Us
This storymap is based on the study published in Environmental Science & Technology titled "Water Resource Recovery Facilities Empower the Electrolytic Hydrogen Economy". Please cite us if you find this page or the paper useful!